Holiday shipping delays are commonplace both for e-commerce firms trying to ship parcel packages to customers via UPS, FedEx and USPS, and with trucking firms moving full and partial truckloads of freight from distribution centers to stores.
Many retailers are struggling to maintain inventory levels for a variety of reasons, but the end result is fewer choices and higher prices for consumers.
Here we’ll take a look at why holiday shipping delays are so commonplace and worse this year than in the past.
Overwhelming Freight Volume
At its core, the freight market is heavily supply and demand based, with increased volume and less transportation capacity currently which means more shipment delays and more expensive freight movements. During the holidays and peak season, freight volume essentially overpowers the availability of transportation. Typically the trucking side of the industry is hit hard with volume first as this is freight that will head to distribution centers and stores to then be sold, whereas the parcel freight industry has a later peak season, as this is typically freight that consumers are ordering and being shipping from the distribution center to individual consumers.
Parcel carriers like USPS, FedEx, and UPS are expecting massive waves of freight volume through the holidays, and simply do not have the capacity to move it, which results in delays.
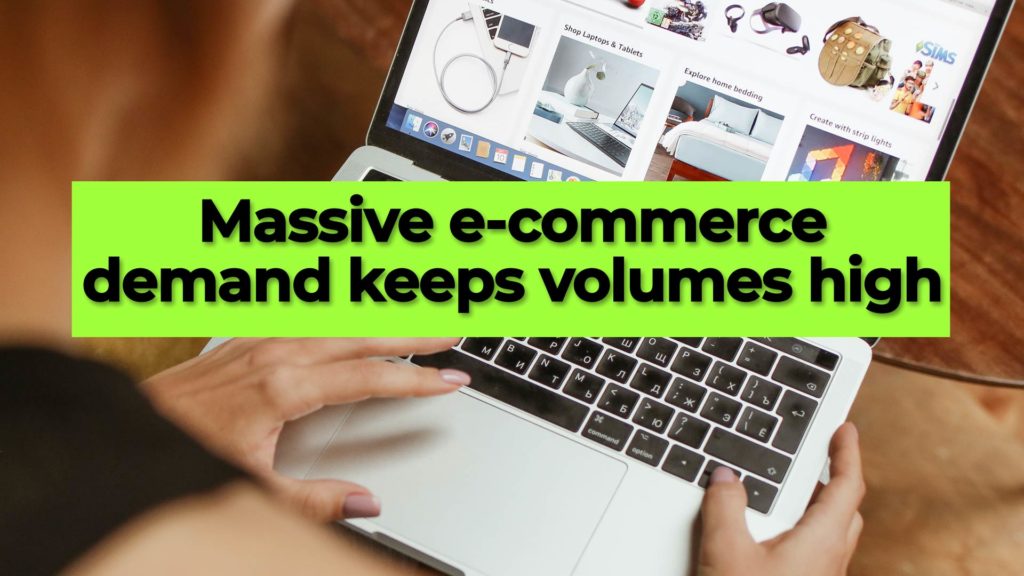
Truckload carriers, ocean freight providers, drayage firms, etc also have similar issues and many brands proactively try to import the majority of their holiday inventory in the late summer to avoid congestion and get the inventory to the various warehouses and stores where it will be sold.
The big takeaway from this section is that if you are a brand, proactively plan for delays, communicate estimated volumes clearly to your logistics and carrier partners, and ship as early as possible.
For consumer brands and e-commerce stores, it’s important to manage expectations with your customers, warning them of possible shipping delays. This will generally help avoid frustrated customers and negative reviews written in anger from slow shipping. Even retail giants like Amazon will have shipping delays within their prime program.
Historically following New Years, supply chain freight volumes drop and carrier networks are able to rebalance during this period of relative down time. However, since the covid pandemic, shipment volumes have not characteristically dropped following Christmas/New Years, as brands struggle to build inventory levels back up to desired levels and delays are so bad that holiday freight is still moving well into January.
Delays in Loading/Unloading
Covid outbreaks in warehouses and distribution centers also create significant delays within your supply chain and increase costs. There were several instances early in the pandemic of meat packing centers having covid-19 outbreaks which necessitated a temporary shutdown or operating at a much reduced throughput resulting in increased prices and lower supply volume. Many small and medium companies rely on third party warehouse and distribution partners, and an isolated covid outbreak can mean your freight stops moving.
More general staffing difficulties have hit many warehouse and distribution facilities beyond covid outbreaks, and this is another challenge that supply chain and facility managers will need to deal with in order to keep freight moving.
As we’ll discuss more later, incorporating technology such as connected cloud-based warehouse management systems, transportation management systems and visibility solutions can provide your receiving team with more accurate information on when freight will arrive and let your team better prepare to efficiently receive freight. This will cut down on demurrage charges as well.
Port Delays
As has been well publicized, there are numerous continuing delays at ports on both the Atlantic and Pacific ports. At the time of this article, there are a shade under 80 ships waiting around the San Pedro bay, which provides a staging ground for ships waiting to enter the Port of Los Angeles or the Port of Long Beach.
Progress is slowly being made to unstick the clog in the US’s port systems, but it’s not an overnight fix. It requires a concerted effort not only from the ports, but also from trucking firms to keep containers moving to the next destination after being unloaded from a ship. The next “stop” for the containers could be the final receiver, a distribution center, a transload center where the freight will be moved into domestic 53 ft containers, or even a rail ramp where the containers will move further inland via railroad service.
These delays mean that freight is simply sitting on ships waiting outside ports, the delays will be compounded down through the rest of the supply chain, with the end result being that for many imports, it’s taking an additional month or so just for the freight to be available at the US delivery point.
West coast ports have increased the fines to customers for not picking up their containers in a timely manner, all in an effort to maintain network fluidity as total container volumes remain high.
Containers
The shipping backlog means that containers are hard to source for exporters wishing to load the empty containers with their own freight to then be sent overseas. This has been a significant frustration for US ag businesses which export a significant portion of their products. Resulting in large delays and increases in cost to get their product to market.
Technology to Reduce Supply Chain Delays
There are instances where technology can be deployed to help alleviate these delays through a number of means. The most basic in concept, is shipment location tracking. Ocean shipping firms do not always have the best and most accurate information on when a ship will be unloaded etc, so tech firms are able to fill this void and provide more accurate/ up to date tracking which lets the beneficial cargo owner, logistics partners, and facilities managers be more prepared for when the cargo will arrive. This means less time is wasted once the container becomes available to be moved out of the port, and drayage firms can proactively plan their capacity around moving what is available.
An intermodal booking platform, which Zmodal offers, can also provide shippers with additional capacity beyond their standard over-the-road dry van providers. By leveraging intermodal for the domestic portion of the trip, long haul trucking costs can be avoided as intermodal is generally 10-25% less costly on lanes longer than 500 miles and it’s a source of transportation capacity that is less volatile and more guaranteed than over the road options. Mode diversification within your supply chains can effectively reduce both risk and cost for freight movements.
Want a free lane and cost savings analysis? – Get in Touch!
Zmodal is a top intermodal shipping company providing door-to-door intermodal, and full truckload services nationwide throughout our digital supply chain dashboard which provides easy route searching, booking, document management, and analytics. CONTACT US if you want to lower your supply chain costs or want access to North American intermodal capacity.