Crazy is an understatement for supply chains and disruptions in 2020. With only a few more months of the year, 2020 has proven to be one of the toughest years in recent memory for supply chain managers and firms globally.
Here are some of our top supply chain tips for 2020.
1. Don’t Put all your eggs in one basket!
Resiliency is so important and can come in many forms, whether that means relying on multiple vendors and suppliers, multiple transportation and shipping partners, multiple modes of transportation, it helps your business to survive disruptions and maintain operations at some level of normalcy. Brands both small and large learned that lesson the hard way in 2020, with companies even as large as Apple, Nike, and Mazda scrambling to readjust their factory production footprint on a global scale. Think long and hard about the risks associated with relying on a single factory/supplier, single transportation partner, and mode of transportation. By far the most common changes firms are making in 2020 are a combination of increasing the supply chain diversification and better-integrating technology.
2. Plan Ahead
It’s not always easy to forecast accurate demand levels, but the latest software systems are getting pretty good at it, at least good enough to give more lead time to factories and logistics partners. This will reduce issues across the supply chain and reduce the risks of inventory shortages.
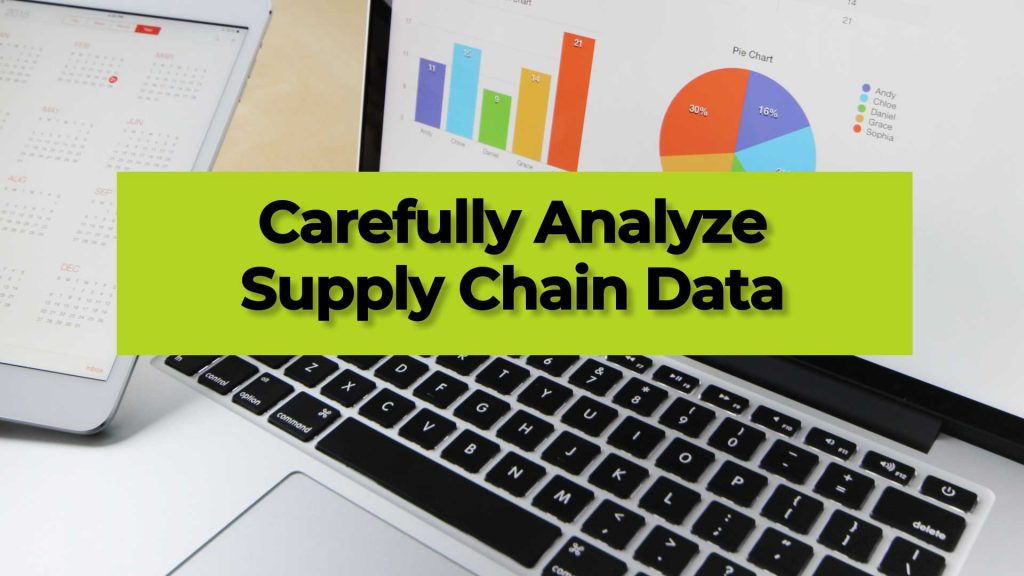
3. Analyze Transportation Spend
Logistics and Supply chain costs have been highly volatile throughout 2020, and that likely won’t change for the remainder of the year or even into 2021. All reports suggest trucking capacity to remain firm for the foreseeable future. If you are seeing your transportation spend rise by 50% or even more, you need to take a look at alternatives. Many firms prefer to stay firmly in the spot market, however, if logistics costs like this are encroaching on your bottom line, you will need to take actions to hedge transportation costs. This can come in many forms, but consider incorporating 3, 6, or 12 month locked in capacity, which means you will guarantee a transportation a certain volume per month or week in exchange for having rates locked in over a period of time. Keep in mind this is a hedge but doesn’t always guarantee you will be paying less, just that the rates won’t change. Mini-bids that focus on monthly or 3 month intervals can help to give some predictability to freight spend. Incorporating intermodal on long haul lanes can reduce spend by 10-25% on many cross country or long haul lanes. Intermodal can be accessed through the spot market, or through a guaranteed capacity/ contract pricing as well. Other strategies to reduce spend involve shipment volumes, lead time, and where the inventory is being held.
A valid strategy would be to move materials in larger volumes to a leased or third-party warehouse as close as possible to your end users. The bet here would be that buying transportation in bulk now is cheaper than the holding costs of inventory in a warehouse. Also, FTL can often be cheaper than LTL.
4. Personnel Needs
Building clear processes and procedures are critical to making sure your team is on the same page and can effectively execute your supply chain plan. Remote working throughout the pandemic has also created a unique situation in which teams are more dispersed and more reliant on technology to address potential disruptions. As a manager or business owner, making sure your team has the resources and information they need to be efficient is critical to the overall success of your business.
This will be a trend going into 2021 as well, but remote working is likely here to stay in part. Many firms will need to make adjustments to better allow for remote operations. Focus on clear documentation of all aspects of your supply chain with a focus on contingency planning, with specific contact details and anything else needed. This provides a continuation of operations if someone is sick, allowing for another team member to temporarily fill in their role.
5. Technology
We’ve indirectly touched on technology, but tech adoption has been rapid for many supply chains through 2020. When possible, your supply chain should leverage technology to automate processes, increase visibility, increase the accuracy of forecastings and inventory management, and to provide better communication between all your team members and logistics partners.
As freight prices have risen so rapidly throughout 2020, many supply chains have turned to digital freight providers to quickly give them quoting and access to capacity they otherwise wouldn’t have. This has given shipper a relief valve and let them keep freight moving when otherwise they would have paid even more exorbitant rates or simply had to wait to move their freight.
Technology is one of the key differentiators between resilient, efficient supply chains and supply chains that need help. It’s easy to get stuck in a rut of doing something in a specific manor over the years, but this is counterproductive to your firm in the long run. Take a look at the most time-consuming supply chain tasks, or the tasks which require the most “guesswork”, then search for potential tech solutions to address these challenges. You’ll be surprised how much time and money you can save by adopting better technology.
6. Import Tariffs and Duties
With the passing of the USMCA agreement in the summer of 2020, NAFTA was officially replaced by an updated trade agreement, which most agree is an effective agreement with more considerations given to technology and intellectual property. If you import large amounts of products or raw materials, work with your logistics partners to analyze how the new USCMA agreement affects your financial performance. It may make sense, depending on your industry, to consider nearshoring in Mexico or Canada. Major firms are also looking at Mexico as an attractive alternative to China for factory production. While China will remain a top trading partner, nearshoring does have numerous advantages including easier management, reduced lead time and transportation cost and less political risk.

7. Make Sustainability a Priority
Firms will be pushed overtime to be more and more sustainable and many larger firms are taking a serious stand to improve supply chain sustainability. We’ve seen factories, warehouses and other facilities add solar panels, more efficient HVAC and lighting. Product packaging is also a consideration, as firms are trying to reduce the use of plastic and overall packaging volume. Taking even small steps can lead to a much greener supply chain over time and reduce supply chain spend by reducing the volume and weight of added packaging. Another initialize is using analytics to reduce fuel consumption through a supply chain, many times this means incorporating intermodal on long-haul lanes, which reduces greenhouse gas emissions by 75%, and better planning truck routes to improve fuel consumption.
What’s Next?
Supply chains have come to the forefront of discussion as many have experienced empty shelves in stores, and lack of inventory from many stores. 2020 has been a strong test of supply chains’ resiliency, problem-solving ability, and procedures. One of the most important actions to take in the remaining months of 2020 is to carefully document what has worked, what hasn’t worked, data analytics and issues. These notes should become a playbook for your firm’s supply chain. In the unfortunate occurrence of another disruptive event, such as a natural disaster, political confrontation, transportation partner issues, etc, you have a documented plan that your employees can rely on to make sure your supply chain remains functional.
About Zmodal
Zmodal is a digital logistics provider, with easy access to North American trucking and intermodal rail service options all through our easy to use dashboard. Search routes, pricing, and book a load within minutes, all while featuring data analytics, digital document management, and full shipment visibility.
Comment